Flotation
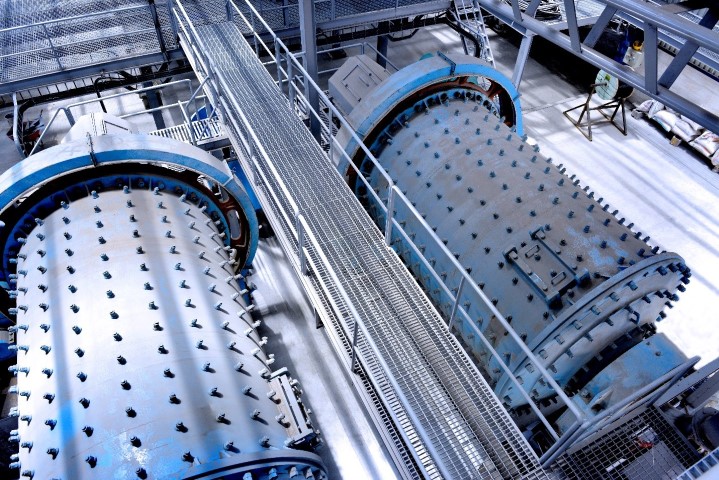
Flotation: A Key Method in Mineral Processing, Particularly for Copper Extraction
Introduction Flotation is one of the most important and widely used methods in mineral processing, especially for the extraction of copper from ores. This process is specifically employed for the separation and purification of minerals from waste materials or tailings and is particularly effective for minerals such as chalcopyrite, chalcocite, and malachite in the copper industry. In this article, we will examine the flotation process, its mechanisms, and its specific applications in copper mining.
The Flotation Process
Flotation is a chemical method used to separate minerals based on their surface properties. This process includes the following stages:
1-Ore Preparation: Initially, the ore is crushed and ground to reduce it to smaller particles. This increases the surface area of the minerals, facilitating their interaction with the chemicals used in the flotation process.
2-Addition of Chemicals (Reagents and Activators): After comminution, chemicals are added to the slurry. These chemicals include reagents (which cause the target minerals to attach to air bubbles), activators (which enhance the performance of reagents), and depressants (which reduce the adherence of non-target minerals).
3-Pulping and Introduction of Air Bubbles: The mixture is then transformed into a slurry and transferred to a flotation cell. At this stage, air bubbles are introduced into the slurry. The target minerals (such as copper) attach to the surface of the air bubbles and rise to the top, while the tailings remain at the bottom of the cell.
4-Collection of Floated Minerals: The target minerals that adhere to the bubbles rise to the surface and are typically collected by skimmers. These enriched minerals are then sent to the next stage of processing.
5-Disposal of Tailings: The tailings, which remain at the bottom of the cell, are discharged from the system.
Application of Flotation in Copper Mining
In copper mining, flotation is particularly used for the extraction of copper from sulfide and oxide ores. The most significant copper minerals separated by this method include chalcopyrite (CuFeS₂), chalcocite (Cu₂S), and malachite (Cu₂(CO₃)(OH)₂).
1-Flotation of Sulfide Minerals: In copper mines with sulfide minerals, flotation is typically performed using specific reagents and chemicals that cause copper minerals to adhere to air bubbles, separating them from other minerals. For example, xanthates and dithiophosphates are commonly used reagents in this process.
2-Flotation of Oxide Minerals: For copper oxide minerals, such as malachite and azurite, the flotation process may require specific adjustments. These adjustments include the use of different chemicals and alterations to process conditions to improve the efficiency of separation.
Advantages of Flotation in Copper Mining:
1-High Efficiency: Flotation can effectively separate a high percentage of target minerals from tailings, contributing to increased recovery rates and improved copper concentrate quality.
2-Flexibility: This process can be adapted for different types of minerals and mining conditions and is applicable to various copper ores.
3-Cost Reduction: The use of flotation as an efficient separation method can help reduce extraction and processing costs.
Challenges and Issues:
1-Environmental Pollution: The use of chemicals in flotation may lead to water and environmental pollution. Therefore, proper waste management and chemical usage are of critical importance.
2-Energy Costs: The flotation process may require high energy consumption, particularly during the comminution and grinding stages of ore processing.
3-Process Condition Adjustments: The success of the flotation process depends on accurately adjusting process conditions, such as pH and temperature, and optimizing chemical usage, which requires precise monitoring and control.
Conclusion:
Flotation is one of the most effective techniques for copper extraction from ores, utilizing the surface properties of minerals to enable the separation of target minerals from waste materials. Despite existing challenges, this method plays a crucial role in the mining industry, particularly in copper processing, due to its high efficiency and flexibility. By improving technologies and properly managing the process, maximum efficiency and minimal environmental impact can be achieved.
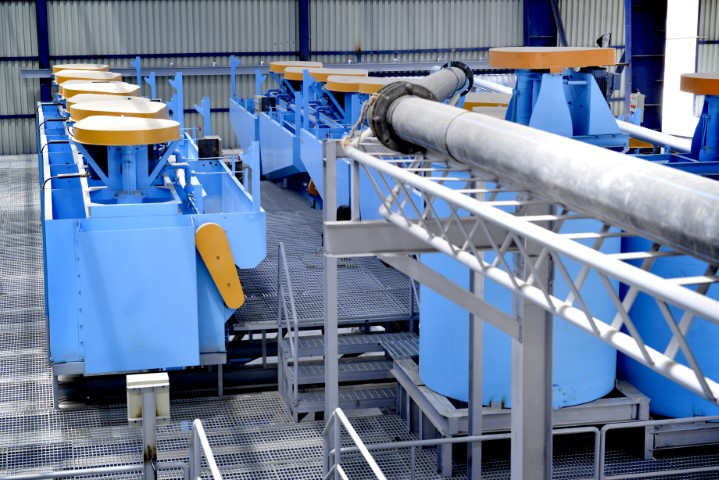